IDENTIFICATION NUMBER 2264
ENTRY CATEGORY (2)
ENTRANT ROLE (Designer /Engineer/ Fabricator and Installer)
APPLICATION OF PROJECT: Restaurant roof, recycled water collection and décor
PROJECT NAME: Trinity Point Tension Membrane Structure 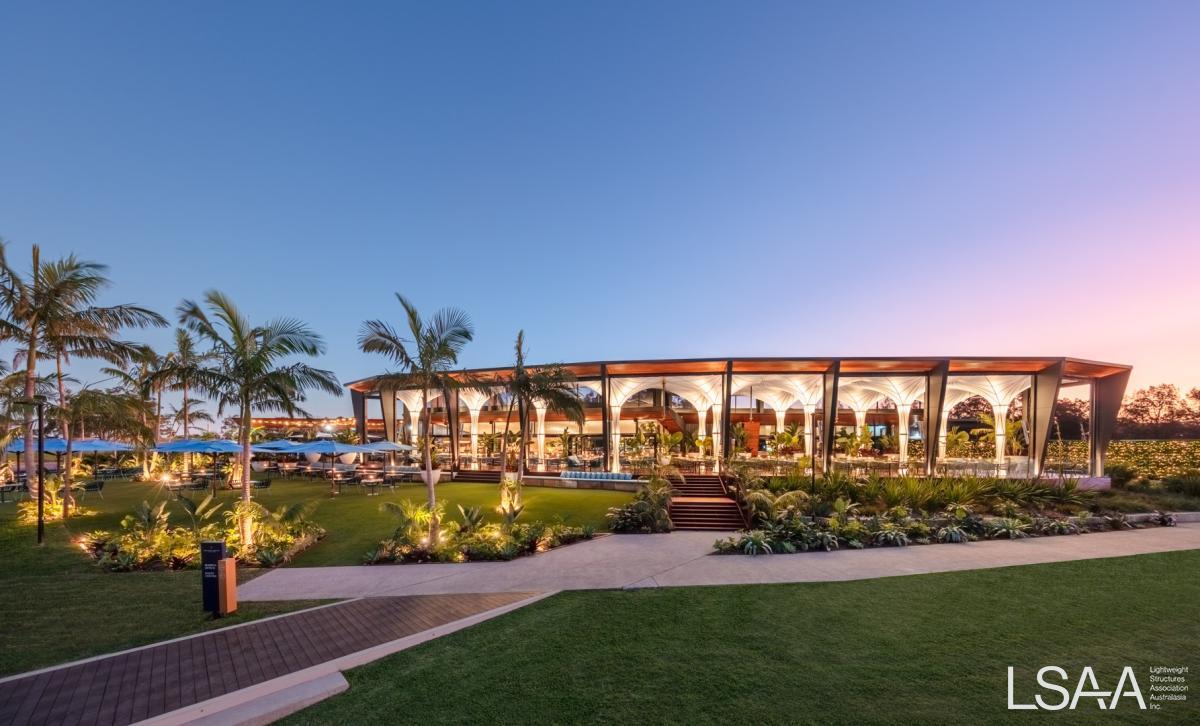
PROJECT DESCRIPTION:
This project was located in the Central Coast of New South Wales. It is a unique tension membrane structure designed to create a wow factor for a new restaurant. It was not only designed to create a visual impact, but also to provide extensive coverage to maximise the outdoor dining area table space and increase revenue for the restaurant.
We were approached by the client to bring a design vision to life. The initial vision of the client to produce this project had come to a halt, then we were asked to come on board to use our expertise to bring this project to fruition and create a visual impact that would create global publicity for the restaurant.
The structure itself was designed inside out. The steel frame for the structure was to be on the outside of the tension membrane and be completely concealed by the material. It was also designed to collect water to create a waterfall effect against the tension membrane, to provide recycling opportunities of re-using rainwater that the structure can collect to irrigate a tropical garden.
There was no room for lack of accuracy in design, project management, and quality control during fabrication.
The client was trying to create an outdoor space that could embrace the movement of water and vibrance of light during the day and at nighttime. This structure was not only designed to provide weather protection, but to create a living geometry around all the patrons of the restaurant.
The movement of water on the structure during the rain creates a warm tropical feeling whilst creating a water feature like aesthetic resemblance.
Although not the smallest job we have completed, the installation of this project was probably the most complex project we have been involved in. Building the steel through the fabric was a big challenge. We had a full-time fabric crew during the steel installation, to make sure none of the membrane was damaged during this process. This took extensive focus, and the install was completed without any damage to the membrane.
A lot of time was spent on design methodology. Every step of the installation process was simulated with all involved three times prior to the installation. This meant we sat down for hours on Zoom meetings during Covid lockdowns to talk through every single step to make sure that any components or steps in the process went missed when it came time to install.
As all stages of the steel were being built, manual measures were checked against every steel member to make sure the detail patterning of the membrane would be accurate
The result of all this work was a spectacular vibrant structure, that created beautiful natural light during the day, and a flamboyant illuminated ambience at nighttime.
Fabric selection was also key to this project with several testing processes involved to create the visual effect that was required through lighting and natural light.
The client was delighted and told us how we exceeded their expectations and needs with the end product. Customers walk into the restaurant and ask to be seated outside under this living structure. When they opened the outdoor area to the public in the new area their social media pages went crazy, bringing more and more people into the restaurant to dine creating the publicity the restaurant was after.
DESIGN / FABRICATION / INSTALLATION BRIEF
This project was unique and complex because unlike the majority of tension membranes which are built on top of a steel frame, the structure was built the other way around. All the steel was to be hidden and suspended from a freestanding frame where the columns were protruding through the Conics. This meant that the steel frame had to be craned in and built through the small lower openings of the tension membrane conics. The steel columns for 300mm in diameter and the narrowest part of the conics was 400x400mm.
This also meant the membrane had to be fabricated prior to the steel being installed which meant the design and fabrication of the steel work, along with the patterning of the material needed to be millimetre perfect. It also meant that there was no room for adjustment or any changes to the membrane after the steel was installed. here was no opportunity to provide a survey of the as built structure prior to fabric patterning.
STRUCTURAL SYSTEMS
There was zero room for error in the design and planning process. Every stage of design needed to be triple checked and extensive modelling was completed to make sure that everything would fit. There was only one chance to get this right with no room for mistakes.
There were many challenges on this project. There were several contractors involved so planning had to be at its best. Collaboration with all contractors, designers of all components, fabricators and installers meant that there were twice weekly zoom meetings involving everyone that had a part in the project including electricians, plumbers, fan suppliers, carpenters, steel fabricators, earthworks and installers. Constant and clear communication is key for this project allowing everybody to provide feedback and search for any hiccups that maybe face along the way. If any of these stages dropped off, the project had the potential to be a complete disaster.
MATERIALS
Hiraoka Sundream – a High Translucent PVC was used for this project. The high translucency of this material was perfect for this application. It maximized natural light, provided great contrast to the black strips that were welded to seams. This allowed for a great visual summary of the form finding and complex geometry.
FABRICATION
Another very unique part of this project from a textile fabrication perspective, were the seams on this project. Usually, seams are made subtle in design of membrane structures, however in this case, every single seam on this project had a black welded strip over the top of it. This was to create a feature of the seams and provide a strong contrast between the highly translucent material and the geometric lines of the patterning.
As there were plenty of seams on this project to create the shape, this also meant that there are a lot of intersection points where several seams were coming together in one location. This meant that some detailed fabrication techniques were required to avoid having bunched weld bleeds at these intersections.
Other challenges in fabrication that we overcame were:
- Working with translucent fabric to give the illusion of black wired cable seams.
- complexity of multiple panels creating overlapped joint and intersection points.
- vertical column fabrication with blind welds
- welding additional fabric to seams without compromising stretch or shrink characteristics.
- hot airing joins without compromising translucency of fabric
- creating 90-degree corners using fabric reinforcing and custom tooling to accompany hot air gun.
- fabricating stage two which consists of 8 inverted conical as one piece.
COLLABORATION, CONSTRUCTION AND MAINTENANCE
When taking on projects of this calibre it is important to have access to the specialist in every field. Fortunately, there was a brilliant crew at hand across all aspects of this project who worked in sync and with cooperation to iron out any potential obstacles.
COSTS
Total Project - $350000
Concept design and feasibility – 13%
Detailing – 15%
Fabrication – 35%
Installation and project Management – 37%
COLOUR IMAGES